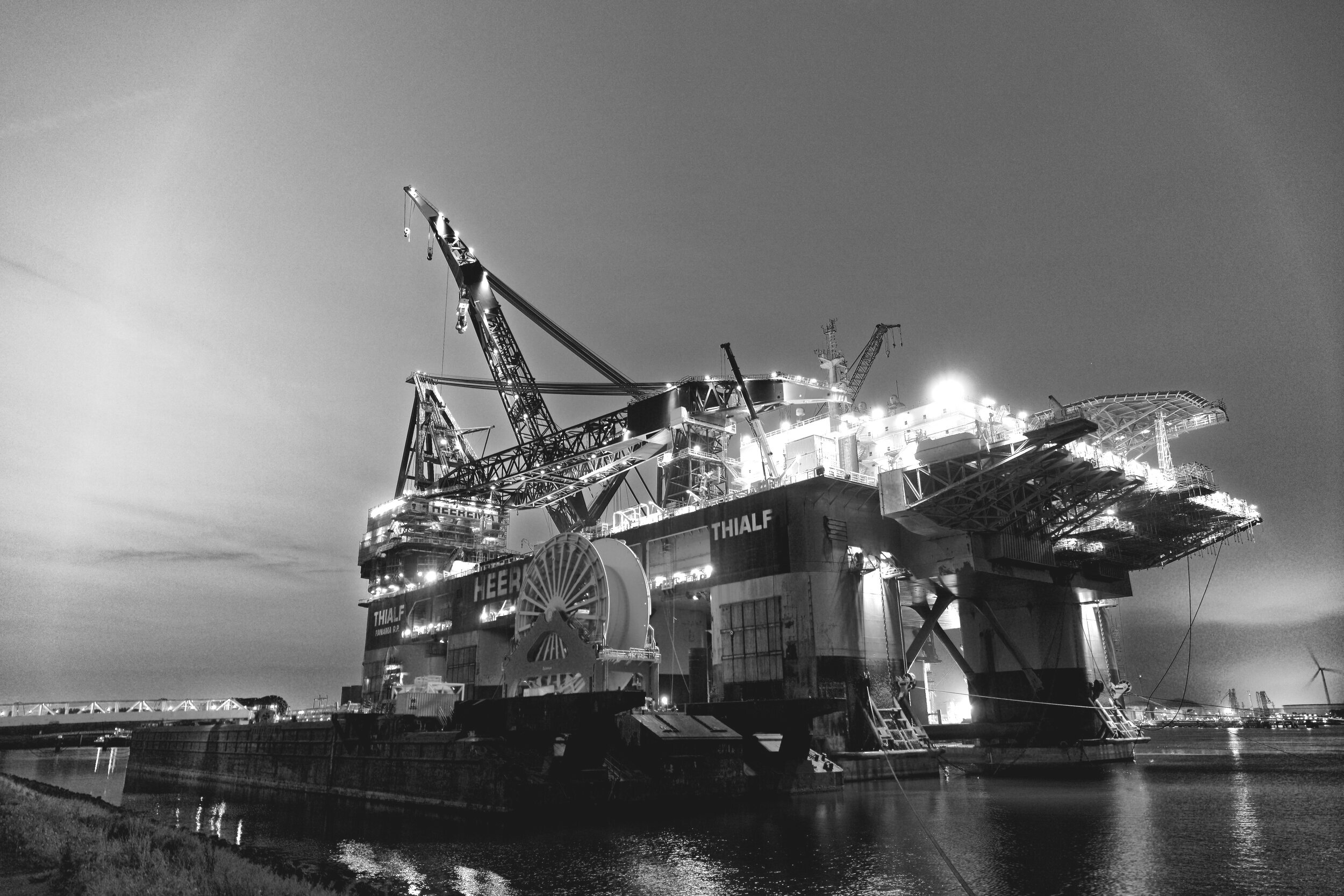
Good outcomes demand that you focus on the results you desire, think innovatively, deliver more and step and repeat success
Today, our customers employ us to improve their asset data. We help them increase productivity by finding accurate data faster, share and rationalise spare parts inventories, accelerate operational readiness, optimise maintenance and inspection planning and construct digital twins.
We do it at a fraction of the time and cost compared to traditional approaches.
IT’S ALL ABOUT THE DATA
All too often the asset data you need is dispersed across legacy documents and systems, isn’t accurate, consistent, up to date or fully recorded. Worse still it may reside in the memories of your staff or some spreadsheets on a local hard drive.
At best you waste 20% of your organisation’s time searching for and validating data. Very often it is much more due to errors, inconsistencies, missing data and poor numbering. Mistakes get made because it’s difficult to see the whole picture, increasing risk. Maintenance and improvement projects are more difficult and take longer.
You cannot capitalize on new technologies because your data is unstructured and not digitally available.
We provide solutions to improve your technical data and make it easier and faster to search, map, link, compare and use. We complement your existing systems and populate them with good data. We DO NOT replace your systems or build yet another database application, locking data up in a proprietary system.
Typical customer use cases
Digitally Intelligent Documents
Especially suited to data handover between project stages and brownfield and modification projects. Provides full content extraction with tag to document linkage and tag/attributes data consolidation. Enables fast access to accurate data via documents, tags, systems, equipment types etc.
Inventory optimisation
Often, data describing inventory is held as unstructured data in ERP systems, making it difficult to match spare parts requirements. This leads to duplication and difficulty in sharing inventory. Making this unstructured data intelligently searchable can reduce inventory levels and make parts much easy and faster to find.
Document Control Assistant
Reduces document control effort >50% by automating check-in and extraction of document meta-data. Performs QC checks on readability and conformance to drawing standards; Performs design checks on document content, tagging and numbering conformance. Catches and corrects faster and earlier.
Digital Twin
A Digital Twin predicts the operational performance of an asset, and enables virtual interaction. To act on predictions you need actionable asset data. This can only be achieved with accurate asset data with tag to document and tag to 3D visual linking. Digitally intelligent documents makes this easy to achieve.
Commissioning & Asset Registers
Developing commissioning packs, and asset registers is a time consuming task involving manual data extraction and mark-up of drawings. Significantly reduces time to extract tags, and data from key documents to assist compiling commission packs, asset registers and maintenance hierarchies.
Proposals
One of the most time consuming tasks at the proposal stage is estimating equipment and materials. Often this is done by manually counting tags from drawings. Reduce effort and time to validate estimates and design data by automating material take-offs and checking tag registers against bid documents.
Asset Verification
Data comes from different sources. Often it is duplicated, inconsistent and difficult to verify. Once captured as intelligent data it can be analysed, checked and consolidated to create a unified view of the technical data. Then it can be mapped, linked and verified with maintenance and material data.
Inspection Planning
Inspection planning means combining data from different sources - line lists, P&ID’s, isometrics, vessel data sheets, material specifications and process condition data. Then it needs to be re-purposed to support a risk based inspection strategy. Combining intelligent documents with rule based learning makes this process faster, with better results with less cost.
our customers







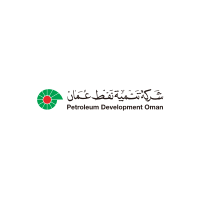


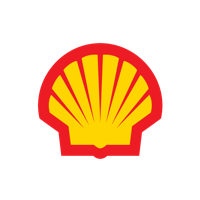






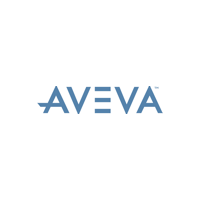
case studies
Inventory Sharing for O&G Operators
The ‘New Normal’, there is no normal! In industries with complex assets that need to run continuously for decades a critical performance indicator is how well they are maintained. This means managing hundreds of thousands of spare parts.
In the oil and gas business in Western Australia a group of operators came up with the idea of sharing inventory stocks to reduce cost and risk.
Data handover for Basrah Gas
Basrah Gas Co. (BGC) is in the middle of an ambitious and challenging development program involving the rehabilitation and rejuvenation of legacy gas processing facilities in southern Iraq.
BGC’s commitment it to achieve world-class operational standards and data is key. The old approach of manual data-scraping is too costly, too time-consuming, and too error-prone.
Flange Management for Petronas
The PETRONAS RAPID project required a single flange register to be created from multiple contractor 3D models and as-built isometrics for around 1,000,000 flanges.
560,000 mixed format CAD and as-built isometrics buried in completion dossiers, needed to be mapped sheet to sheet and then flange to flange. To do this manually would take too long and was too complex.